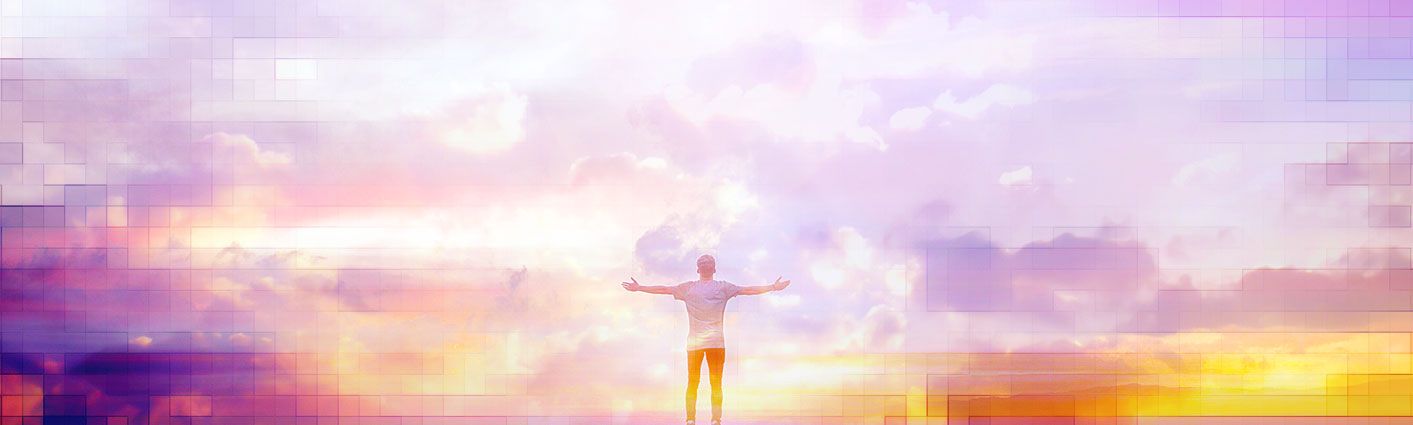
Making Alarm I/Os Smarter – Part 2
This series of blog posts highlights some of the more advanced features found in the new Optima NEXUS nano and RIO xR3 Remote Terminal Units (RTU).
This second installment provides a look at the alarm threshold handling capabilities common to both models. The article builds upon some of the topics already introduced in PART 1.
ALARM THRESHOLDS
OVERVIEW
Our goal was to offer improved alarm handling flexibility. Towards that end, all RIO xR3 multi-mode hybrid inputs, and all NEXUS nano analog input/discrete contact inputs can be programmed:
- with their own unique sets of alarm thresholds,
- with their own sets of qualification timers,
- with their own sets of extended labels, to make alarms more descriptive.
Most alarm handling devices on the market today only allow for two severity levels per input:
- NORMAL, and
- a user defined ALARM level.
Many times custom coding is required to extend these capabilities. Especially when an application demands more than flipping between these two basic states. In our new RTUs, we now offer an upper and a lower set of thresholds. Each set consists of separate INFO, WARNING, MINOR, MAJOR, and CRITICAL thresholds.
We let the user decide, individually per I/O, which of these thresholds are enabled or disabled. Thereby, the utmost flexibility without the need for custom coding/scripting is achieved. The following section will go through setting up all of the parameters, step-by-step.
PARAMETERS
Individually controlled ON/OFF CHECK-BOXES. Allows the user fine grained control over each threshold.
Simply remove the check-mark from any threshold that will not be required.
Indicates the SEVERITY LEVEL selected for each ‘band’ or range. The MINOR, MAJOR and CRITICAL ranges can be further graded on a scale from 1 to 9.
This allows fine-tuning the three most essential alarm levels. Use the scale from 1 to 9 to either elevate or downgrade one alarm compared to the rest of the I/Os in the same range. Or use the default level 5 if no special grading is required at this point.
Specifies the analog signal LEVEL at which this threshold will be crossed.
All threshold values must be located between the upper and lower brackets (maxima).
With the QUALIFICATION PERIOD, the user controls how long a signal must stay above or below the corresponding threshold in order to be considered valid.
If the signal retreats back before the qualification timer has run out, no action will be taken (as the qualification period was not met).
An alarm message may be generated once the signal has been above (or below) the threshold level for the minimum amount of time specified by the QUALIFICATION PERIOD.
Select the proper time SCALE for the specified QUALIFICATION PERIOD.
The following time scales are available:
- 0 to 1000 milliseconds (in steps of 5 ms),
- 0 to 240 seconds,
- 0 to 240 minutes, or
- 0 to 240 hours.
Use the BASE LABEL EXTENSION to specify a more descriptive label which will be sent along with every alarm notification once the corresponding alarm threshold has been crossed.
NOTE: The extension label will be added to the base label of the I/O. Maximum length: 40 characters.
Example:
BASE LABEL: Main Site Access Door
BASE LABEL EXTENSION: has been open for more than 5 hours
Result:
The following string will be sent as part of each alarm message caused by crossing the selected threshold:
Main Site Access Door has been open for more than 5 hours
INPUT PROCESSING
Each input is processed as follows:
- The input signal is conditioned, digitized and cleaned up.
- The obtained value is processed by the analog front end, applying the GAIN, OFFSET, SCALE, BIAS, QUANTIZER settings, as well as the UPPER and LOWER LIMITS.
- The result of the previous stage is then further formatted according to the OUTPUT FORMAT template.
- The UNIT STRING is added.
- Next, the user specified THRESHOLDS are applied.
- Once a threshold has been crossed, the specified QUALIFICATION TIMER or LEVEL TIMER is started.
- Once the TIMER has run out, the signal may be deemed valid.
- The ADAPTIVE ALARM SUPPRESSION (AAS) settings, if enabled, are applied.
- If the event has passed the AAS tests, an alarm event notification will be created and LOGGED.
- Next, logged event notifications must pass the ALARM THROTTLING (if enabled).
- If it passes the ALARM THROTTLING stage, the RTU SENDS out the ALARM to the programmed recipients.
DEFAULT SETTINGS
By default, none of the thresholds are enabled (see screen-shot above). Consequently, the entire input range is defined as the NORMAL range:
BASIC EXAMPLE
In this basic example, we will only enable one threshold. Here are the basic parameters we have chosen for this example:
INPUT RANGE:
MINOR THRESHOLD:
HYSTERESIS:
QUALIFICATION PERIOD:
0 Vdc to 60 Vdc
@ 40 Vdc
5 Vdc
50 ms
Observe how the corresponding graph changes in real-time:
The resulting graph has been split into two ranges. The MINOR alarm range extends from just above 40 Vdc to 60 Vdc. The NORMAL range goes from 0 Vdc up 40 Vdc. On the right hand side, the deltas corresponding to each range are shown.
In the center, we can see the effect of the HYSTERESIS. Once in MINOR alarm, the input level will have to fall back down to 35 Vdc to be able to clear the alarm condition.
This provides the crucial separation between the alarm range and the normal range. It keeps the I/O from toggling unnecessarily.
Specifying a suitable HYSTERESIS avoids the dreaded alarm chatter, which can be caused by input levels hovering just around the values specified by an alarm threshold.
Additionally, by specifying a QUALIFICATION PERIOD of 50 ms, we can further ensure that any crossing of the threshold lasting for less than the time specified by the QUALIFICATION PERIOD will be ignored.
ADVANCED EXAMPLE
The next paragraphs pick up where PART 1 of this series left off. Initially, we had specified a set of parameters to condition an input. Ultimately, this resulted in a value ranging from 0 – 100%, in 10% increments. Now, let’s have a look at how we could go about slightly tweaking the output, and then adding a whole set of escalating thresholds:
OVERALL INPUT RANGE:
STEP SIZE:
NORMAL RANGE:
INFO RANGE
WARNING RANGE
MINOR RANGE
MAJOR RANGE
CRITICAL RANGE
HYSTERESIS:
QUALIFICATION PERIOD:
0% to 100%
5%
100% down to 75%
75% down to 50%
50% down to 35%
35% down to 20%
20% down to 10%
10% down to 0%
2.5%
various
Here is how the corresponding graph changes in real-time:
The resulting graph has been split into six ranges: NORMAL, INFO, WARNING, MINOR, MAJOR, and CRITICAL. Although they operate on a descending input value level, they carry an increasing severity. This is due to the fact that the lower the level in the fuel tank is dropping, the more important it becomes to take corrective action.
Again, on the right hand side, the deltas corresponding to each range are shown.
In the center, we can see the effect of the HYSTERESIS. Once in a certain alarm range, the input level will have to rise back up above the THRESHOLD + HYSTERESIS in order to clear each alarm range.
This provides the crucial separation between the individual alarm ranges. It keeps the I/O from flipping back and forth unnecessarily. Specifying a suitable HYSTERESIS avoids the dreaded alarm chatter, which can be caused by input levels hovering just around the values specified for each alarm threshold.
Additionally, by providing suitable QUALIFICATION PERIODs, we can further ensure that any crossing of a particular threshold lasting for less than the time specified will be ignored.
ALARM LABELS
Since we have one BASE LABEL EXTENSION per alarm threshold, we can specify much more descriptive alarm labels to be carried in each alarm notification.
Optima firmly believes that the less cryptic an alarm message, the higher the chances that the true importance of the message will be be understood, and acted upon.
Here is the complete list from the above example, showing the resulting label.
NOTE: Keep in mind, these are suggestions only. These fields are user specified. They can be used to carry other details, such as recommendations for remedial actions or contact details.
The final result consists of the BASE LABEL (defined once per I/O), plus each BASE LABEL EXTENSION (one for each alarm/normal range).
BASE LABEL:
NORMAL RANGE:
INFO RANGE:
WARNING RANGE:
MINOR RANGE:
MAJOR RANGE:
CRITICAL RANGE:
Tank A Fuel Level
Tank A Fuel Level is normal
Tank A Fuel Level just below normal
Tank A Fuel Level heads-up: low level detected
Tank A Fuel Level fell below minor threshold
Tank A Fuel Level fell below major threshold
Tank A Fuel Level is now critically low
SUMMARY
The flexibility offered by the NEXUS nano and RIO xR3 analog inputs processing stages allow even complex operations to be carried out on an input signal without the usual need for custom coding or scripting. The example above clearly highlights the power of the available parametric interface. The web-based Optima GUI turns even advanced setups with escalating severity settings into straightforward point-and-click operations.
OUTLOOK
The upcoming 3rd installment in this series will focus on the whole set of Optima’s enhanced time based alarm controls. Stay tuned.

Ralf Doewich
Optima Tele.com, Inc.